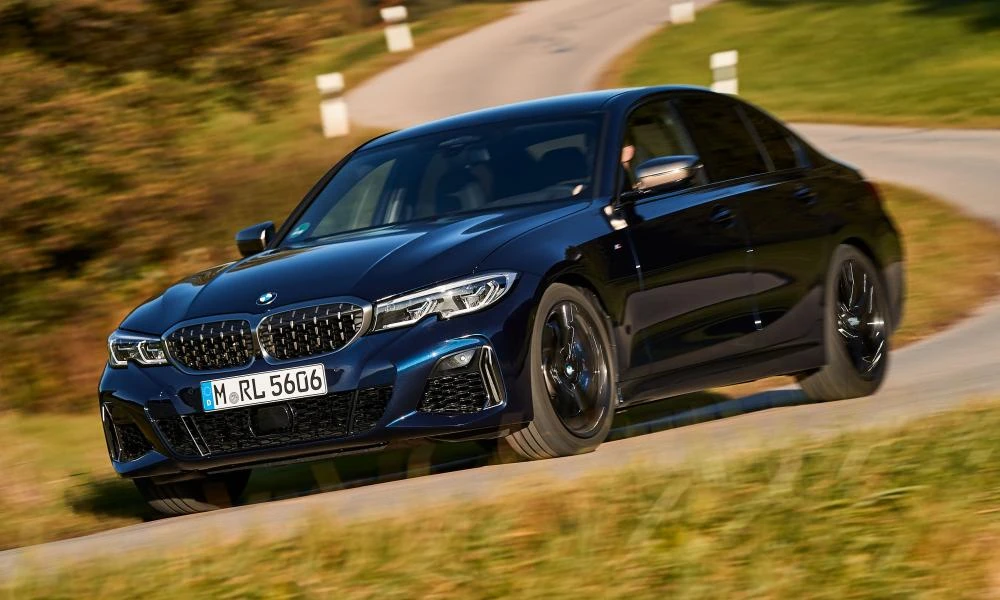
Η προγνωστική συντήρηση, που στηρίζεται σε ένα έξυπνο σύστημα παρακολούθησης, προβλέπει και προλαμβάνει πιθανές βλάβες στον εξοπλισμό. Οι αναλύσεις δεδομένων του εξοπλισμού μεταφοράς επιτρέπουν τον έγκαιρο εντοπισμό προβλημάτων, βοηθώντας έτσι στη διατήρηση βέλτιστης ροής στην παραγωγική διαδικασία των οχημάτων.
Το σύστημα που χρησιμοποιεί τεχνητή νοημοσύνη (AI) εμποδίζει κατά μέσο όρο περίπου 500 λεπτά διακοπής ετησίως στη συναρμολόγηση οχημάτων στο εργοστάσιο του Ρέγκενσμπουργκ.
Πόσο πάει το μαλλί; Tο ενεργειακό κόστος της τεχνητής νοημοσύνης
Ανάλυση δεδομένων για ταχύτερη απόκριση σε πιθανές διαταραχές
Για τη συναρμολόγηση στο εργοστάσιο του BMW Group στο Ρέγκενσμπουργκ, τα οχήματα τοποθετούνται γενικά σε φορητές βάσεις φόρτωσης ή σε συστήματα ολίσθησης που κινούνται με αλυσίδα, τα οποία διέρχονται από τις αίθουσες παραγωγής. Οποιοδήποτε τεχνικό σφάλμα στα υπερσύγχρονα συστήματα μεταφοράς μπορεί να οδηγήσει σε ακινητοποίηση των γραμμών συναρμολόγησης.
Αυτό αυξάνει τις απαιτήσεις τόσο σε επίπεδο συντήρησης όσο και κόστους. Για να αποφευχθεί αυτό, η ομάδα καινοτομίας του εργοστασίου του Ρέγκενσμπουργκ ανέπτυξε ένα σύστημα που μπορεί να εντοπίζει έγκαιρα πιθανά τεχνικά προβλήματα – και έτσι να αποφεύγονται τυχόν απώλειες στην παραγωγή.
Τα επηρεαζόμενα εξαρτήματα του στοιχείου μεταφοράς μπορούν να αφαιρεθούν από τη γραμμή συναρμολόγησης και να επισκευαστούν μακριά από την παραγωγή. Το πλεονέκτημα είναι ότι το σύστημα παρακολούθησης δεν απαιτεί πρόσθετους αισθητήρες ή εξοπλισμό, αλλά αξιολογεί τα υπάρχοντα δεδομένα από τα εγκατεστημένα εξαρτήματα και το σύστημα ελέγχου των στοιχείων μεταφοράς. Αν διαπιστωθούν ανωμαλίες, ηχεί συναγερμός.
Για παράδειγμα, οι βάσεις φόρτωσης που χρησιμοποιούνται για τη μεταφορά οχημάτων στη γραμμή συναρμολόγησης αποστέλλουν διάφορα δεδομένα στο σύστημα ελέγχου του μεταφορέα, τα οποία διαβιβάζονται στη συνέχεια μέσω αυτού και της μονάδας ελέγχου του εργοστασίου στην πλατφόρμα προληπτικής συντήρησης του BMW Group που βασίζεται σε cloud. Από εκεί ξεκινά η ανάλυση:
Ο αλγόριθμος αναζητά συνεχώς παρατυπίες, όπως διακυμάνσεις στην κατανάλωση ενέργειας, δυσλειτουργίες στις κινήσεις του μεταφορέα ή barcode που δεν είναι επαρκώς ευανάγνωστα, που θα μπορούσαν να προκαλέσουν προβλήματα. Εάν αυτά εντοπιστούν, το κέντρο ελέγχου συντήρησης λαμβάνει ένα προειδοποιητικό μήνυμα, για το οποίο ενημερώνεται ο τεχνικός συντήρησης που έχει βάρδια. «Οι οθόνες παρακολούθησης στο κέντρο ελέγχου λειτουργούν 24 ώρες το 24ωρο», εξηγεί ο υπεύθυνος έργου Oliver Mrasek. «Αυτό μας επιτρέπει να ανταποκρινόμαστε γρήγορα σε κάθε είδους αναφορά σφάλματος και να απομακρύνουμε το όχημα που επηρεάζεται από τον κύκλο της διαδικασίας».
Υλοποίηση – υποστηριζόμενη από την τεχνητή νοημοσύνη
Η προγνωστική συντήρηση δεν είναι μια αυτοδύναμη λύση, τονίζει ο Mrasek. Το σύστημα τυποποιήθηκε σε συνεργασία με την κεντρική διοίκηση της μονάδας παραγωγής του BMW Group και άλλων εγκαταστάσεων, ώστε να μπορεί να εφαρμοστεί άμεσα και σε άλλα εργοστάσια του ομίλου ανά τον κόσμο. Αυτή η προσέγγιση είναι επίσης οικονομικά αποδοτική. «Δεν χρειαζόμαστε πρόσθετους αισθητήρες, οπότε το κόστος αφορά μόνο την αποθήκευση και την υπολογιστική ισχύ».
Μοντέλα μηχανικής μάθησης που αναπτύχθηκαν εσωτερικά εφαρμόστηκαν στο σύστημα, το οποίο χρησιμοποιεί τους λεγόμενους θερμικούς χάρτες με διάφορους χρωματικούς κωδικούς για τις διάφορες ανωμαλίες για την οπτικοποίηση των ευρημάτων του μοντέλου. «Αυτό μας επιτρέπει να χαρτογραφήσουμε διαφορετικά μοτίβα σφαλμάτων σε διάφορα εξαρτήματα και να ανταποκριθούμε σε αυτά με στοχευμένο τρόπο», εξηγεί ο Mrasek.
Με βάση αυτά τα πρακτικά ευρήματα, οι αλγόριθμοι βελτιώνονται και τελειοποιούνται συνεχώς. Η ομάδα βρίσκεται επί του παρόντος στη διαδικασία σύνδεσης πρόσθετων εγκαταστάσεων, βελτιστοποίησης του συστήματος και ενσωμάτωσης των συνιστώμενων ενεργειών στα μηνύματα σφαλμάτων. Αυτό θα μπορούσε, για παράδειγμα, να υποδεικνύει παρόμοια προβλήματα που έχουν εμφανιστεί σε ένα σύστημα απλοποιώντας την αντιμετώπισή τους για τους τεχνικούς συντήρησης – για παράδειγμα, αν μια φτερωτή σε ένα καρότσι μεταφοράς είναι ελαττωματική. «Η βέλτιστη προγνωστική συντήρηση, πέρα από το οικονομικό όφελος, μας βοηθά να παραδώσουμε έγκαιρα την προγραμματισμένη ποσότητα οχημάτων – γεγονός που μειώνει τρομερά το άγχος στην παραγωγή», εξηγεί ο Deniz Ince, επιστήμονας δεδομένων της ομάδας.
Επόμενος στόχος: Προβλεψιμότητα – και δύο διπλώματα ευρεσιτεχνίας
Ο Mrasek και οι συνάδελφοί του εργάζονται τα τελευταία έξι χρόνια στην παρακολούθηση της τεχνολογίας των συστημάτων μεταφοράς βάσει δεδομένων. Σήμερα, περίπου το 80% των βασικών γραμμών συναρμολόγησης παρακολουθείται ήδη με αυτόν τον τρόπο. «Φυσικά, δεν μπορούμε να εντοπίσουμε ή να αποτρέψουμε κάθε πρόβλημα εκ των προτέρων – αλλά αυτή τη στιγμή γλιτώνουμε τουλάχιστον 500 λεπτά διακοπής λειτουργίας ετησίως μόνο στη συναρμολόγηση οχημάτων», εξηγεί. Είναι εύκολο να υπολογίσετε τι σημαίνει αυτό. Στο εργοστάσιο του BMW Group στο Ρέγκενσμπουργκ, ένα όχημα βγαίνει από τη γραμμή συναρμολόγησης περίπου κάθε λεπτό -για την ακρίβεια κάθε 57 δευτερόλεπτα – και το σύστημα χρησιμοποιείται ήδη σε συστήματα μεταφοράς στις εγκαταστάσεις των εργοστασίων στο Ντινγκόλφινγκ, τη Λειψία και το Βερολίνο.
Μητσοτάκης: Η Ελλάδα να αποτελέσει ένα παγκόσμιο κέντρο της τεχνητής νοημοσύνης
Στόχος είναι η περαιτέρω αξιοποίηση των δυνατοτήτων της τεχνητής νοημοσύνης, με το σύστημα να μαθαίνει να εκτιμά πόσος χρόνος απομένει από τη στιγμή ανίχνευσης της βλάβης μέχρι μία πιθανή διακοπή λειτουργίας. Αυτό θα βοηθούσε τους τεχνικούς να αποφασίζουν πόσο σύντομα πρέπει να εκτελούν τις εργασίες συντήρησης αλλά και να προτεραιοποιούν τις ενέργειές τους, αν χρειάζεται. Ο Mrasek βλέπει επίσης περαιτέρω προοπτικές και σε άλλους τομείς του εργοστασίου: «Τώρα, εξετάζουμε επίσης τη δυνατότητα χρήσης του συστήματος στον εξοπλισμό που χρησιμοποιείται για την πλήρωση των οχημάτων μας με υγρό φρένων και ψυκτικό μέσο, για παράδειγμα».
Αν και υπάρχουν ήδη πολλές επιλογές για την προγνωστική συντήρηση του εξοπλισμού, το ολοκληρωμένο σύστημα εκμάθησης του Ρέγκενσμπουργκ είναι, μέχρι στιγμής, το πρώτο του είδους του. Επομένως, η συμβατότητα με την προγνωστική συντήρηση έχει ήδη εγγραφεί στις προσφορές που αφορούν τις τεχνολογίες μεταφοράς. Οι κατασκευαστές εξοπλισμού επαινούν επίσης το σύστημα, καθώς επωφελούνται και οι ίδιοι από τις αξιολογήσεις του. Το BMW Group έχει ήδη κατοχυρώσει δύο διπλώματα ευρεσιτεχνίας για την ανάπτυξή του εσωτερικά.